What Is Value Engineering
Why should I care?
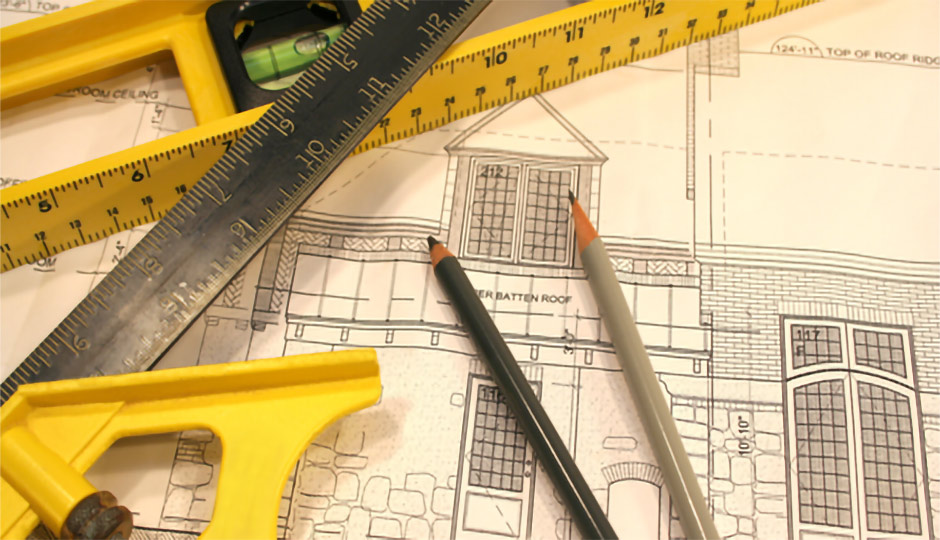
We hear the term “Value Engineered” a lot, but are you really getting the full “Value” out of your engineer or architect? If you truly want your project to be value engineered, it’s a good idea to hire an experienced engineer and get him or her on board before the design in complete. It is fairly easy for an experienced engineer to be able to look at some preliminary floor, elevation and section plans and identify areas that may be costing you money that need not be spent. In this climate we receive extreme snow loads, high winds and have the potential for substantial earthquakes (which we have to design in conjunction with a portion of the snow load) requiring a great deal of engineering to make work. An experienced engineer will have done literally hundreds of projects in this climate, and becomes quite good at spotting areas in the design that will cost a lot of money to make work.
TIMBER COSTS
Your engineer must first be familiar with, or know where to get the answers of, the current rough costs of the different lumber that can be used on a project. Take roof rafters for example. We have a variety of choices, each of which has its positive and negative properties. Some of the choices are Rough Sawn Lumber, Trusses, Timberstrand, Parallams, Microllams, Wood I-Joists, Boise Cascade products, TJI products, Steel, SIP’s (Structurally Insulated Panels), etc. We as engineers also need to know the rough installation costs, for some of these products need to be modified in order to work or require some hardware to make work, or may just have a very labor intensive construction cost. It is important to consider these choices as the project is being designed, that is if you want to stay in budget.
DESIGN FLEXIBILITY
Take for example an open living room / kitchen with a tight budget, a vaulted ceiling and a 12:12 roof pitch. Most people like to have the 12:12 interior vault which requires a ridge beam and rafters that can span between the ridge beam and supporting walls. The ridge beam will typically be a Glue Laminated Beam or a Steel I-Beam, depending on the size of the room costing anywhere from 3-$10k. If the room is wide enough, the rafters will likely be Microllams or equal costing 8-$18 / Lineal Ft. You could see the price for that vaulted living room can spiral out of control. Now if you want to save some money and are okay with a 6:12 interior vault, you could use scissor trusses and cut costs nearly in half.
Other areas that we typically look at are the shear walls. An experienced engineer can quickly look at the floor plans and elevations and determine which of the shear walls will work with conventional lumber (2x6 studs and 15/32” APA rated sheathing i.e. plywood). If there are not enough of these shear walls available, we then have to look at other options such as Steel Moment Frames, that can easily be $10k per story or Simpson Strong Walls that are much more expensive than conventional shear walls. A lot of the time
slight tweaks to the window openings and obtain the required walls without detracting from the architect’s vision.
The Value Engineering does not stop at the end of the design process. Value Engineering should continue all the way through the rough frame portion of construction. One way to save is for the engineer to be open minded in his or her responses to field questions or suggestions from the contractor. The contractor may have a better way to frame an area or transfer loads that could save significant time and money, but it must be approved by the Engineer of Record. Being open minded to these ideas will help economize the final product. It is also very important to respond to contractor questions quickly because time is money in the field and a lagging engineer can definitely hold up the process.